Call :
PENTA Call 1
Project status :
Completed
Project website :
http://www.cosmodu.eu
Key application areas





Essential capabilities

Connectivity & Interoperability




PARTNER
AMITRONICS Angewandte Mikromechatronik GmbH / Advanced Packaging Center BV / Berliner Nanotest und Design GmbH / Boschman Technologies BV / Catena Holding BV / Delft University of Technology / Fairchild Semiconductor / Fraunhofer Institute for Electronic Nano Systems / Fraunhofer-Gesellschaft - IISB / Heliox / Langer EMV-Technik GmbH / Robert Bosch GmbH / Siemens AG / Technolution BV
AMITRONICS Angewandte Mikromechatronik GmbH / Advanced Packaging Center BV / Berliner Nanotest und Design GmbH / Boschman Technologies BV / Catena Holding BV / Delft University of Technology / Fairchild Semiconductor / Fraunhofer Institute for Electronic Nano Systems / Fraunhofer-Gesellschaft - IISB / Heliox / Langer EMV-Technik GmbH / Robert Bosch GmbH / Siemens AG / Technolution BV
Countries involved
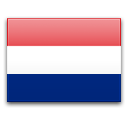

Project leader(s)
Kai KriegelKey project dates
01 October 2017 - 30 September 2020CosmoDU stands for smart, efficient integrated industrial drives with communication and self-learning capability for connected systems.
The evolution of machines requires electric drives to actively monitor and adjust their own key operational parameters such as speed, direction and power, in case of performance or environmental changes. CosmoDU has developed the hardware platform of next-generation drive units, where sensors, signal processing, secure communication and control and power electronics have been directly integrated in the housing of the motor. This new drive unit uses its self-learning capabilities to adjust and improve its performance.
Background, objectives of the project and faced challenges
Today industrial drives consist of electric motors, inverters, and an additional control stage. Maintenance is done regularly independently from load and system condition. The smart intelligent electric drives developed within CosmoDU will be key enablers for Industry 4.0. They will increase manufacturing flexibility and even have the ability to learn and to communicate. Moreover, they will maximise system availability by eliminating downtime due to unexpected servicing needs. The objective was to develop a hardware platform which integrates sensors, signal processing, secure communication and control electronics as well as the power electronics and the driver stages directly in the housing of the motor. The platform should be used for different applications as conveyor belts, robotics, tooling machines, automated driving and full-scale electromobility, as well as smart energy and smart infrastructure solutions. Together with functional performance, CosmoDU has addressed multiple challenges such as electro-magnetic compliance (EMC), thermal management, functional safety and system availability that specifically arise from an ultra-compact design. Indeed, fast switching power devices in the neighbourhood of low voltage components tend to cause EMC issues, while the limited cooling capability of the integrated system is highly demanding in terms of thermal management.
Technological achievements
System architecture
The CosmoDU consortium developed a modular hardware architecture for the integration of sensor, micro and power electronics modules to fit into the housing of a motor drive. A clear partitioning of functions is accomplished by considering the severe requirements related to thermal management and EMC. The architecture enables full integration of the inverter and the sensors for health monitoring and drive performance optimisation. All information is shared throughout the motor and with the higher system layers using a standard for data exchange (OPC UA). This provides a scalable and manufacturer independent way to disclose information towards the higher layers of the control and monitoring system.

SiC power modules
Saving energy is one key element in the efforts to reduce global warming. The use of new silicon carbide (SiC) semiconductors in inverters allows to significantly reduce conduction and switching losses compared to silicon (Si) based power semiconductors. The higher power density and higher temperature capabilities of SiC components were addressed with a power module design for dual side cooling. Better heat transfer and new assembly techniques enable to achieve not only good operational performance but also high reliability.

Condition and health monitoring
Each CosmoDU motor is equipped with its own thermal impedance spectroscopy (TIS) board, allowing to determine the health status of the power modules. The CosmoDU sensor module constantly records motor vibrations as well as sound and provides those data together with motor parameters to the Local Decision Controller. These data gathered in a feature vector are transferred to higher control levels, either to the Central Decision Controller or to the Cloud, for self-learning analysis. This allows the customers to replace components before they fail.

Secure wireless communication
The Wireless communication module shows a performance clearly surpassing the IEEE 802.11ac Wifi standard requirements, particularly in terms of reception quality and associated power usage. Moreover, the successful proper functioning of a prototype IEEE802.11ah Wifi system was shown in an industrial environment under harsh conditions regarding interferences, strange propagation path properties, reflections and damping factors between factory compartments with heavily disturbing motors.

Integrated smart motor drive
The motor is a series servo motor, on which the electronics housing is mounted. The electronics housing contains the high voltage power electronics as well as the low voltage control, sensor, and communication boards. The compact motor drive unit allows a versatile usage. The wireless communication link, the smart health monitoring and process diagnostics are especially beneficial in systems with decentralised drives, e.g. conveyor belts. The CosmoDU motor serves as sensor and communication hub of other adjacent components of an installation.

Market Potential
CosmoDU is targeting to deliver a smart hardware platform for next generation electric drives with high efficiency, performance optimisation and health monitoring used in industrial automation systems. The total market for industrial power trains relevant to industrial drives is worth about 25 billion USD, with annual growth of over 10% for drives using conventional technology. With integrated power and IT technology, the market share for intelligent integrated powertrains is expected to grow even faster. More specialised markets are also relevant: e.g. the global conveyor belt market is forecasted to achieve at an annual growth rate of 3.7% during the period 2019-2025, leading to an expected total market size of 5 billion USD in 2025. For this market, the increasing demand partly comes from the mining industry, due to their significant requirements of longer distances, strength, flexibility, easy maintenance, and high-splice strength and safety. Promising demand trends can also be found such in the aviation business, automated production plants or warehousing and logistic systems.
The CosmoDU results will have an impact on the following products:
- Semiconductor, microelectromechanical systems (MEMS) sensors and power modules (ON Semiconductor, Bosch, APC, Boschmann)
- Electrical drives and control platforms (Siemens, Heliox, Technolution)
- Secure Wireless communication (Catena)
Societal & Economic Impact
Smart drives will enable major reductions in energy consumption in factory automation by reducing cabling as well as increasing the overall system efficiency. It is estimated that industrial drives could cut approximately 10% of worldwide electrical energy consumption, with corresponding savings in costs and CO2-emissions. Additionally, CosmoDU project will deliver benefits for its participants – three large companies, eight small and medium-sized enterprises (SMEs) and three research institutes and universities from Germany and the Netherlands. The market-leading original equipment manufacturer (OEMs) and Tier 1 suppliers involved will be able to exploit the results in their businesses. For the expert SMEs, this is an opportunity to employ and develop their expertise in key areas such as electromagnetic compliance (EMC), health monitoring of electronic systems, active performance control, packaging processes and equipment, motor control and system integration of the hardware and software. Similarly, the research organizations will gain valuable knowledge in industrial practice, which will both enrich academic knowledge and improve future research services to industry. CosmoDU will not only strengthen the technological leadership of the involved partners, but also support European manufacturing and create new jobs through competitive, smart and highly flexible industrial production.
Patents/Standardisation/ Publications
The partners actively disseminated the results from CosmoDU project at several domestic and international events and workshops, including EFECS 2017/2018/2019 and Precisiebeurs 2018, in company with various demonstrating components, posters and oral presentations. Representatives of the ECSEL JU Lighthouse initiative Industry4.E have been contacted for additional dissemination opportunities and collaborative options. The project results will be presented with a booth at the EFECS 2020. The project delivered several papers to general public and published various press releases via social media including internal newsletter, partner’s website, LinkedIn and Twitter.
Future Developments
The innovative approaches in CosmoDU are an important step to higher system integration and smarter ICT in the field of industrial automation. For further decarbonization, the number of efficient industrial drives needs to be increased. Moreover, in a sustainable environment a high reliability and a long lifetime are crucial. This means for future developments that the focus on efficient power devices, reliable packaging, compact design, improved 3D system integration, EMC, secure communication and the application of artificial intelligence will be enforced. To meet these goals, new follow-up projects are under discussion.