Project status :
Recently completed
Key application areas



Essential capabilities

PARTNER
Eindhoven University of Technology / Fraunhofer-Gesellschaft zur Förderung der angewandten Forschung e.V. / Neotech AMT GmbH / Philips Electronics Nederland BV / Reden BV / Signify / TNO / VSL BV / Würth Elektronik eiSos GmbH & Co KG / XENON Automation GmbH
Eindhoven University of Technology / Fraunhofer-Gesellschaft zur Förderung der angewandten Forschung e.V. / Neotech AMT GmbH / Philips Electronics Nederland BV / Reden BV / Signify / TNO / VSL BV / Würth Elektronik eiSos GmbH & Co KG / XENON Automation GmbH
Countries involved
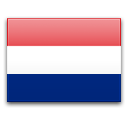

Project leader(s)
Johan KlootwijkKey project dates
April 2021 - July 2024Additive Manufacturing based Production of Embedded Robust Electronics (4D printing) [AMPERE]
Combining Additive Manufacturing (3D printing) and the fourth dimension – the addition of electrical and optical functionalities, AMPERE aimed to enable flexible, reliable production of smart systems with relevance for Industry 4.0 and smart industrial processes. These in turn will allow for new functionalities in areas such as lighting, signal and power electronics, and medical devices.
Achievements and results of the project
The AMPERE project covered three use-cases:
- The (Philips) Lead extraction device:
— Baseline concept: adding the Philips Ultrasound module by Pick and Place on printed 3D structures
— Innovation track: new machine and software were built to fully integrate the structural body printing, pick & place and interconnect printing for functional imaging cores. - The (Signify) LED lighting demonstrators:
— LED spots and LED pendants were realized using 4D printing. - The (Würth) SPE connector:
— Possibility of the basic manufacturing of SPE connectors using hybrid production has been shown.
Background, objectives of the project and challenges
Electronics manufacturing companies face increased challenges due to the constraints of the current manufacturing architecture. A promising solution is the combination of Additive Manufacturing (3D printing) and the fourth dimension – adding electrical and optical functionalities, known as 4D printing. This innovative approach involves printing 3D structures
with additional functionalities, like metal interconnect lines, simultaneously.
The AMPERE project aimed to enable flexible, reliable production of smart systems relevant to Industry 4.0 and smart industrial processes. AMPERE advanced smart design processes and extended the application range to power electronics, moving beyond the current state-of-the-art. This effort helps Europe regain its manufacturing leadership by closely integrating
required processes with the design cycle, creating a world-leading and difficult-to-replicate capability.
Four specific objectives were defined in the AMPERE project:
- Develop and integrate essential technology for scalable hybrid 4D manufacturing that is both flexible and cost-effective. This technology aims to meet industry needs, from small series mass customization to higher production volumes.
- . Realize these advancements through digital smart processes, integrating mechanical, electrical, and optical functionalities in 4D products.
- Develop scalable and reliable industrial production systems using essential technology and smart processes.
- Demonstrate the hybrid 4D manufacturing approach in three innovative product cases across different applications and sectors: LED luminaires, signal and power electronics, and medical devices.
One significant challenge in the 4D printing process was creating the interconnect layer. This layer needed to cover multiple surfaces, handle CTE (Coefficient of Thermal Expansion) mismatch, and provide a low resistive connection. Although new printing materials were developed, some issues arose. The interconnect layer was satisfactory for the LED and signal and
power electronics demonstrators but needed further improvement for the lead extractor device to become fully functional.
For the commercial viability and sustainability of these processes, scalability needs improvement. The aim is to refine these processes to ensure they are sustainable and economically feasible for broader industry application.
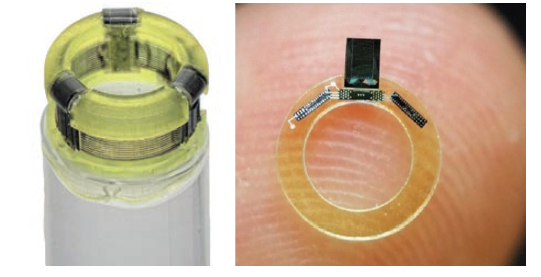
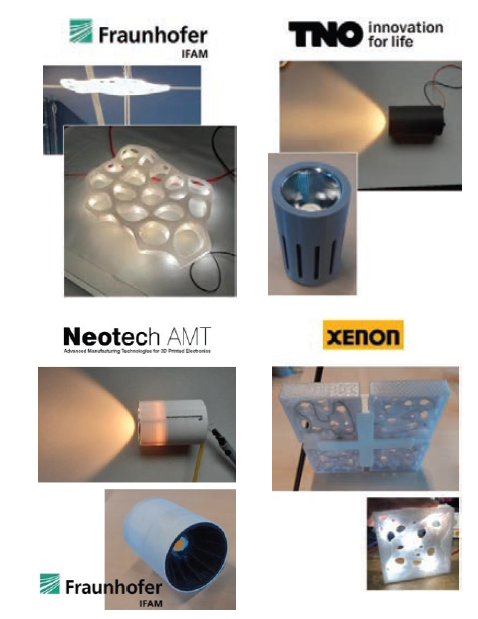
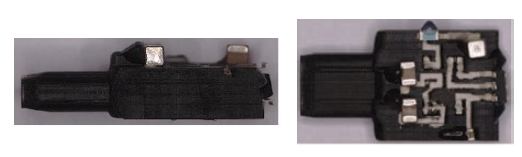
Technological achievements
Close cooperation across the entire value chain was key to achieving AMPERE’s ambitions. The project partners covered the whole range of necessary technical competences, as well as the complete value chain of materials, processes, equipment, product design, manufacturing and applications. This project has provided very valuable results and knowledge. This
helps end users to realize more easily minimal viable products, such that early feedback can be obtained is a very important learning of this project.
To further benefit from the 4D printing approach, we need to reach a certain technological maturity level for widescale adoption, for which AMPERE has definitively shown the potential.
TNO and NeoTech gained a lot of knowledge on the 4D printing process, both technically as well as in terms of sustainable processing.
In addition, insights gained in the AMPERE project have led Neotech to take the initiative to re-develop a CAD/CAM toolpath generator, aiming at a simple user interface enabling easier printing, sort of automatic code generator. In the AMPERE project the developed technology has been demonstrated by different use-cases, from which some photographs are shown in figure 1, 2 and 3. Figure 1 shows some images from (parts) of the lead-extraction device. Although not fully functional, all printing steps have been performed and the full product has been realized. Figure 2 shows some pictures of the LED demonstrators, showing different types of operational LED spots and pendants. Finally, Figure 3 shows some pictures from hybrid manufactured SPE connectors. In order to enable realizing these demonstrators, an essential part of the AMPERE project was (further) development of the printing equipment and new printing materials, thereby also considering environmental impact.
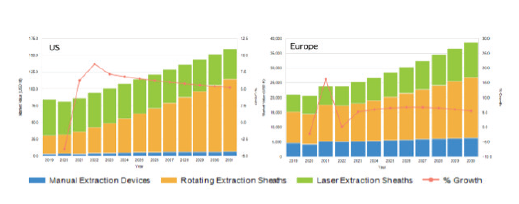
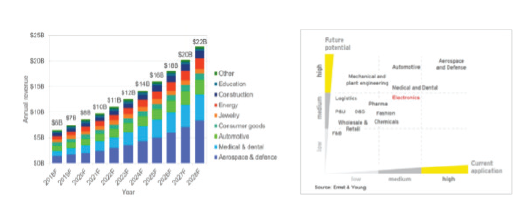
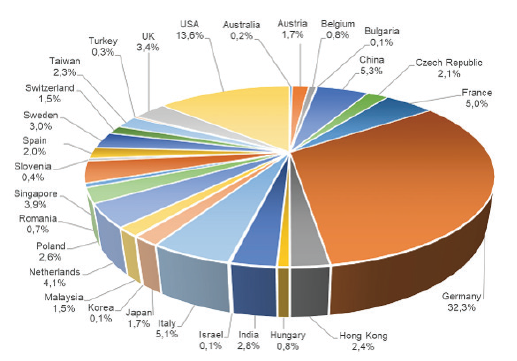
Market Potential
Lead extraction. The lead extraction device market will grow 5% annually, reaching $200 million by 2030. Philips Healthcare, currently holding 75% of the market in the US and Europe, may increase its share to nearly 90%. New ultrasound-guided sheets could boost market growth by 20-30%. Integrating these into the Philips Cathlab suite will strengthen Philips’ dominance.
LED. Electronics is a promising market for additive manufacturing, with high growth potential. Signify’s 2021 turnover was 6.86 billion euros, with 83% from LEDs. If 1% of this turnover is in AM luminaires, it could reach 57 million euros. The LED lighting market forecast for 2026 is 145 billion euros. Growth beyond 100 million euros is possible with increased market share.
SPE. By 2030, the global market for SPE connectors is projected to reach 25 million units. With a market share between 2% and 4.5%, this translates to 500,000 to 1.1 million units. Sales forecasts, based on Würth Elektronik eiSos’s past year sales and market knowledge, predict SPE connector sales starting in 2025. Given the strong growth of passive connectors and their projected market value of 40 billion USD by 2026, the market for SPE connectors is expected to rise. Even capturing 0.1% of this market translates to several hundred thousand units. The new SPE connector is likely to follow a similar distribution as the RJ45 connector.
Societal & Economic Impact
Philips CMUT housing is printed using a prototype 4D printing technology. In its current state it is already projected to be more environmentally friendly than a possible competing technology. Signify LED spot housing when printed with a more mature 4D printing process generates practically no waste during processing and near-unity material efficiency.
The Würth showcase has shown that the basic manufacturing of the SPE connector using hybrid production is possible. The further development of the Pick & Place and camera systems and the programming of the Neotech System 15XSA, had a positive impact on the production of the SPE connector. Towards the future we suggest investigating the use of copper for
4D printed electronics which will reduce the potential greenhouse gas emissions further.
Patents, Standardisation, Publications
A total of 8 General Assembly Meetings have been organized at various partner locations. More than 70 dissemination activities (presentations and publications) were recorded of which the vast majority were presentations at international conferences. An overview of the current state-of-theart in 4D printing-based manufacturing has also been discussed with guidelines
on what areas must be addressed and improved to encourage widescale adoption of this technology. Identified areas of improvement include the need for biobased and recyclable materials, improved dielectric and conductive materials performance, and improved standardisation of design tools to facilitate simplified transition from product design to manufacturing. Next to this several announcements on the Ampere results have been posted on social media, in particular on LinkedIn.
Future Developments
We identified 17 projects across the consortium that are connected to AMPERE. These projects range from development of digital metrological twins to electrical functionalization of PPE.
In addition, discussions are taking place on next steps as a consortium, since we all experienced that we work well as a team! A potential follow-up project may include or encompass sustainability of materials.